中頻加熱爐憑借 “深度熱透能力 + 自動化適配性”,成為圓棒料(如碳鋼、合金鋼、不銹鋼棒)加熱處理的核心設備,尤其配合機床夾具實現自動推送料后,可無縫融入流水化生產線,兼顧加熱均勻性與生產效率,完美滿足批量熱加工需求。
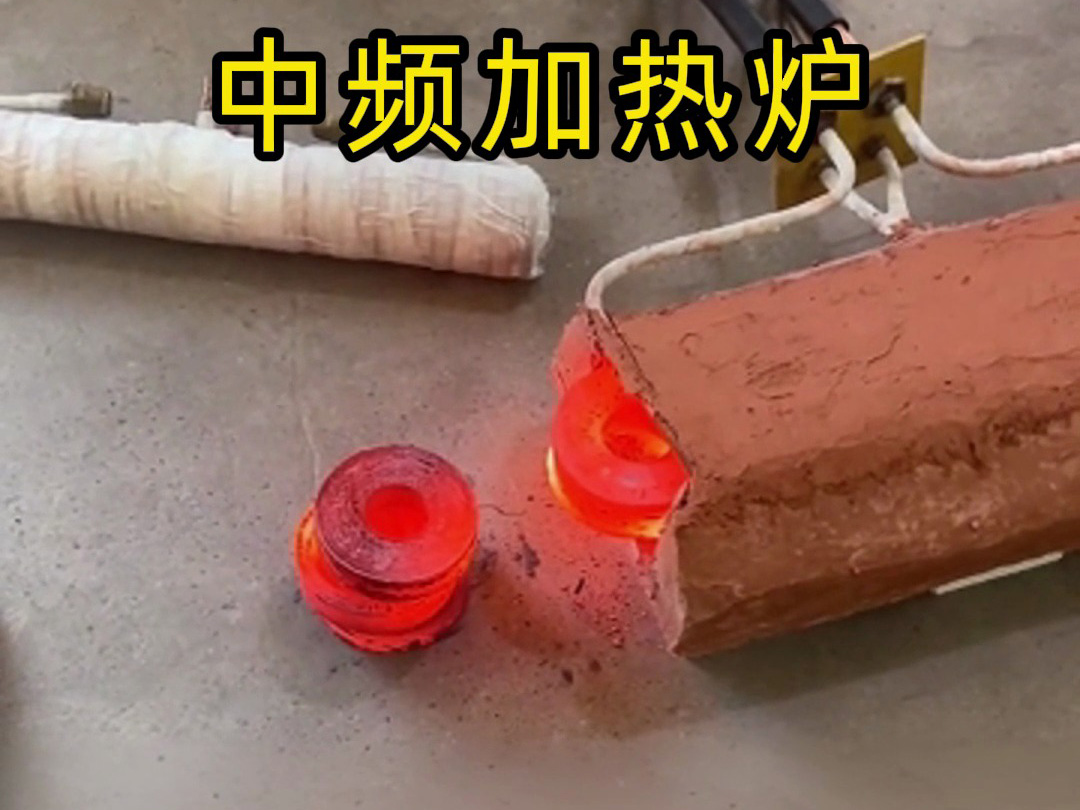
圓棒料的熱加工(如熱鍛、熱彎、熱裝配)需 “整體熱透”(芯部與表面溫差≤50℃),中頻加熱(頻率 1-10kHz)在此展現獨特優勢:
深度加熱,實現全截面熱透
中頻電流的趨膚效應較弱(硬化層深),能量可穿透圓棒料截面(直徑 50-300mm 均可),使芯部與表面同步升溫。例如直徑 100mm 的 45# 鋼棒,中頻加熱至 1100℃(熱鍛溫度)僅需 8-12 分鐘,芯表溫差≤30℃,避免傳統高頻加熱 “表面過熱、芯部未透” 的問題。
溫度均勻,保障熱加工質量
通過線圈環繞式加熱(圓棒料在感應線圈內勻速通過),配合紅外測溫閉環控制,整根圓棒的溫度偏差≤±20℃,長度方向溫度一致性達 95% 以上。熱透后的圓棒料在鍛造時晶粒細化均勻,熱彎時變形量穩定(誤差≤0.1mm/m)。
適配廣,兼容多材質與規格
無論是低碳鋼棒(如 Q235)、中碳鋼棒(45#),還是合金結構鋼棒(20CrMnTi),中頻加熱均可通過調整功率(50-200kW)和加熱時間,實現精準熱透。單臺設備可覆蓋直徑 20-300mm、長度 1-6m 的圓棒料,無需頻繁更換線圈。
配合機床夾具與自動推送機構,中頻加熱爐可實現 “上料 - 加熱 - 出料” 全流程自動化,滿足流水化生產需求:
自動推送料的工作邏輯
上料階段:圓棒料通過料架滾落至推送軌道,由伺服電機驅動的推桿將棒料逐根送入中頻加熱線圈(推送速度 0.5-2m/min,可根據加熱時間調節);
加熱階段:棒料在線圈內邊移動邊加熱(“行走式加熱”),通過線圈長度(通常 1-3m)與推送速度的匹配,確保總加熱時間精準(如熱鍛需 10 分鐘,則推送速度 = 線圈長度 / 時間);
出料階段:加熱完成的棒料自動推送至下一工序(如鍛造機床、熱彎模具),通過溫度檢測剔除不合格品(如超溫或欠溫)。
與流水化生產的無縫銜接
推送機構與后續加工設備(如鍛壓機、校直機)通過 PLC 聯動,實現 “加熱 - 加工” 節拍同步。例如:熱鍛生產線中,中頻爐每 10 秒送出 1 根熱透棒料,鍛壓機同步完成 1 次鍛造,單班(8 小時)產能可達 2800 + 件,較人工上料提升 3 倍。
對比項 | 中頻加熱爐(自動推送) | 傳統燃煤 / 燃氣爐(人工上料) |
---|
熱透質量 | 芯表溫差≤30℃,長度方向均勻性≥95% | 溫差≥100℃,局部過熱 / 欠熱常見 |
生產效率 | 連續流水化生產,單爐日產能 100-500 噸 | 間歇式生產,日產能≤30 噸 |
人工成本 | 1 人監控整條線,無需頻繁操作 | 2-3 人輪換上料、翻料、出料 |
能耗成本 | 熱效率 60%-70%,無燃料浪費 | 熱效率≤30%,爐體散熱 / 煙氣損耗大 |
環保安全 | 電加熱無廢氣,操作區無明火 | 燃煤 / 燃氣產生煙塵、CO,安全隱患高 |
熱鍛行業:汽車半軸圓棒、螺栓坯料的熱透加熱,配合自動鍛壓機實現 “加熱 - 鍛造” 一體化,鍛件晶粒均勻,合格率提升至 99%;
工程機械:挖掘機銷軸、液壓桿圓棒的熱彎前加熱,中頻熱透后彎曲回彈量≤0.5°,無需二次校直;
金屬加工:軸承套圈毛坯、齒輪坯料的熱擴徑加熱,自動推送確保每批料溫度一致,后續加工余量減少 20%。
中頻加熱爐對圓棒料的 “深度熱透” 能力,配合自動推送料的流水化設計,完美解決了傳統加熱方式 “質量差、效率低、污染大” 的痛點。對于需要批量處理圓棒料的行業,這種 “加熱 - 推送 - 加工” 的一體化模式,不僅是產能提升的保障,更是產品質量穩定性的核心支撐,成為現代金屬熱加工流水化生產的 “標配” 設備。