在棒料鍛造生產中,全自動棒料鍛造加熱爐通過流程化設計,將送料、加熱、成型環節無縫銜接,為批量生產提供了穩定高效的熱加工方案。
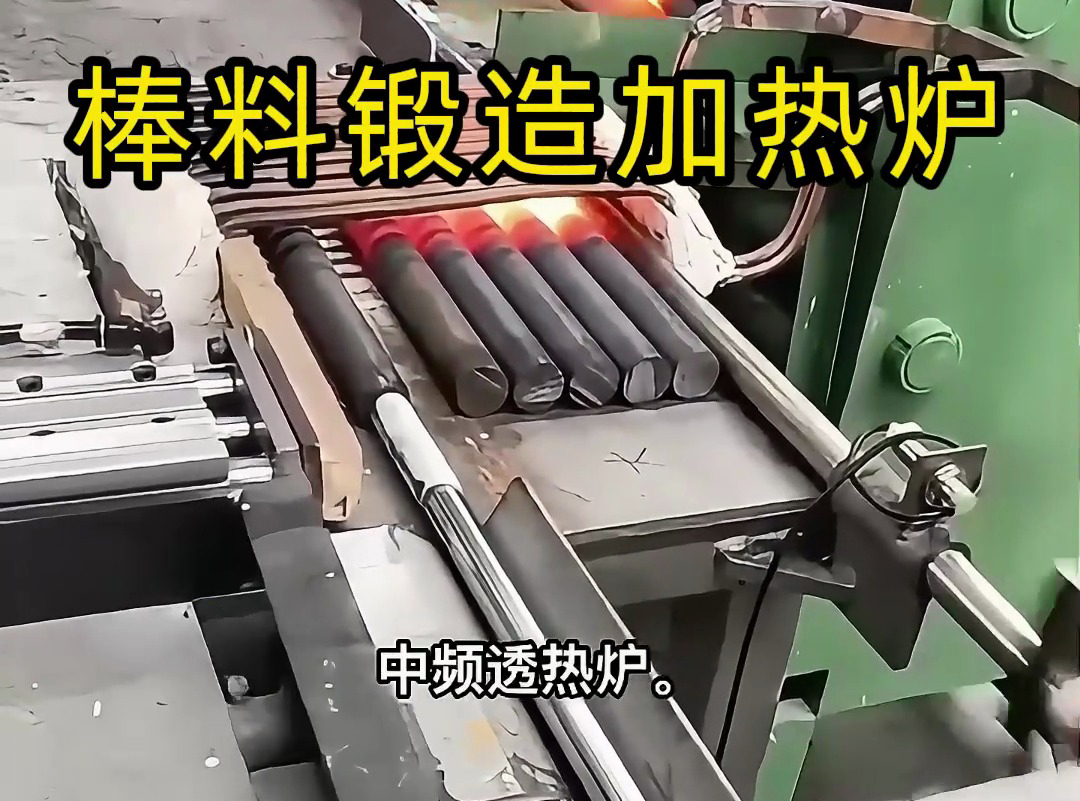
這套設備的核心邏輯在于 “自動化流轉”。送料機作為起始環節,可根據預設的棒料長度(支持直徑 10-80mm 的圓鋼、方鋼)自動上料,通過輸送輥道將棒料精準推送至中頻加熱爐入口。中頻加熱爐(頻率通常 2-10kHz)利用電磁感應原理對棒料整體加熱,根據材質特性調節參數 —— 例如 45# 鋼棒料需加熱至 1100-1150℃,加熱時間隨直徑變化,直徑 50mm 的棒料約需 40 秒,確保芯部與表面溫度均勻(溫差≤50℃)。
加熱完成的棒料由機械夾具快速移送至沖床工位,夾具的定位精度控制在 ±0.5mm 以內,保證沖壓時的位置準確性。整個過程無需人工介入,避免了傳統人工送料時的高溫燙傷風險,也減少了因操作節奏不一致導致的質量波動。

實際生產中,這套系統的效率優勢顯著。以直徑 30mm 的棒料為例,傳統人工線單班產能約 500 件,而全自動設備可達 1200 件以上,且沖壓成型的尺寸一致性更好 —— 經檢測,工件直徑偏差從 ±0.3mm 縮小至 ±0.1mm,廢品率降低至 1% 以下。
設備的適應性也較為靈活,更換棒料規格時,只需在控制系統中輸入新參數(長度、直徑、加熱溫度),調整送料機的截料尺寸和沖床的沖壓力度,15 分鐘內即可完成換型,滿足多品種生產需求。
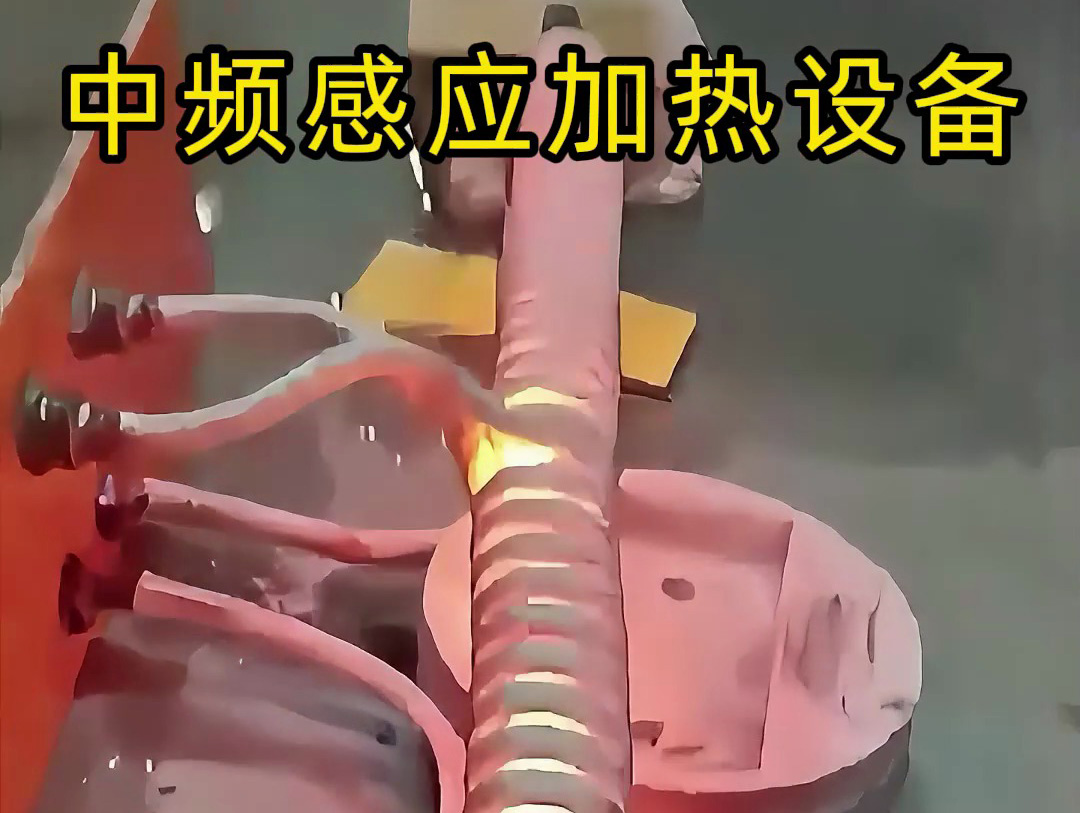
維護方面,需每日檢查送料輥道的對齊度(防止棒料跑偏),每周清理中頻爐內的氧化皮堆積,每月校準加熱溫度(用紅外測溫儀比對設定值與實際值)。按此規范操作,設備的連續運行穩定性可達 800 小時以上。
對于追求批量生產效率與質量穩定性的棒料鍛造場景,這套全自動加熱爐通過各環節的精準配合,既保證了棒料加熱的均勻性,又通過自動化流轉提升了整體產能,成為熱加工領域的實用選擇。