齒輪作為機械傳動的核心部件,需同時具備表面高硬度(耐磨性)與芯部高韌性(抗沖擊),淬火熱處理是實現這一性能組合的關鍵工序。在火焰淬火、感應淬火、激光淬火等多種方式中,高頻淬火設備憑借精準、高效、低變形的優勢,成為齒輪淬火的主流選擇,尤其適配多樣化生產需求。

針對齒輪的齒面、齒根等關鍵部位,高頻淬火(頻率通常 30-100kHz)的優勢顯著:
淬火方法 | 加熱精準度 | 效率(單件處理時間) | 變形控制 | 適用齒輪類型 |
---|
高頻淬火 | 齒面溫差≤±10℃ | 5-30 秒(根據模數) | 變形量≤0.05mm | 中小模數齒輪(m≤6)、精密齒輪 |
火焰淬火 | 齒面溫差 ±50℃以上 | 1-3 分鐘 | 變形量≥0.1mm | 大型齒輪、對精度要求低的齒輪 |
接觸電阻淬火 | 局部易過熱 | 20-60 秒 | 變形較大 | 簡單齒形齒輪 |
激光淬火 | 溫差≤±5℃ | 10-40 秒 | 變形極小 | 超精密齒輪(成本高) |
精準聚焦加熱:通過仿形感應線圈(貼合齒形設計),將熱量集中于齒面、齒根等易磨損區域,加熱溫度精確控制在 850-900℃(齒輪鋼 Ac3 溫度以上),齒芯溫度≤300℃,避免整體性能受損;
高效批量處理:中小模數齒輪(如汽車變速箱齒輪)單件淬火僅需 10 秒,配合自動上下料系統,單小時產能可達 300-500 件,較火焰淬火提升 3-5 倍;
變形微乎其微:高頻加熱時間短(熱影響區小),配合后續低溫回火(180-200℃),齒輪公法線長度變動量≤0.03mm,齒向誤差≤0.01mm/m,無需二次校直即可滿足裝配精度。
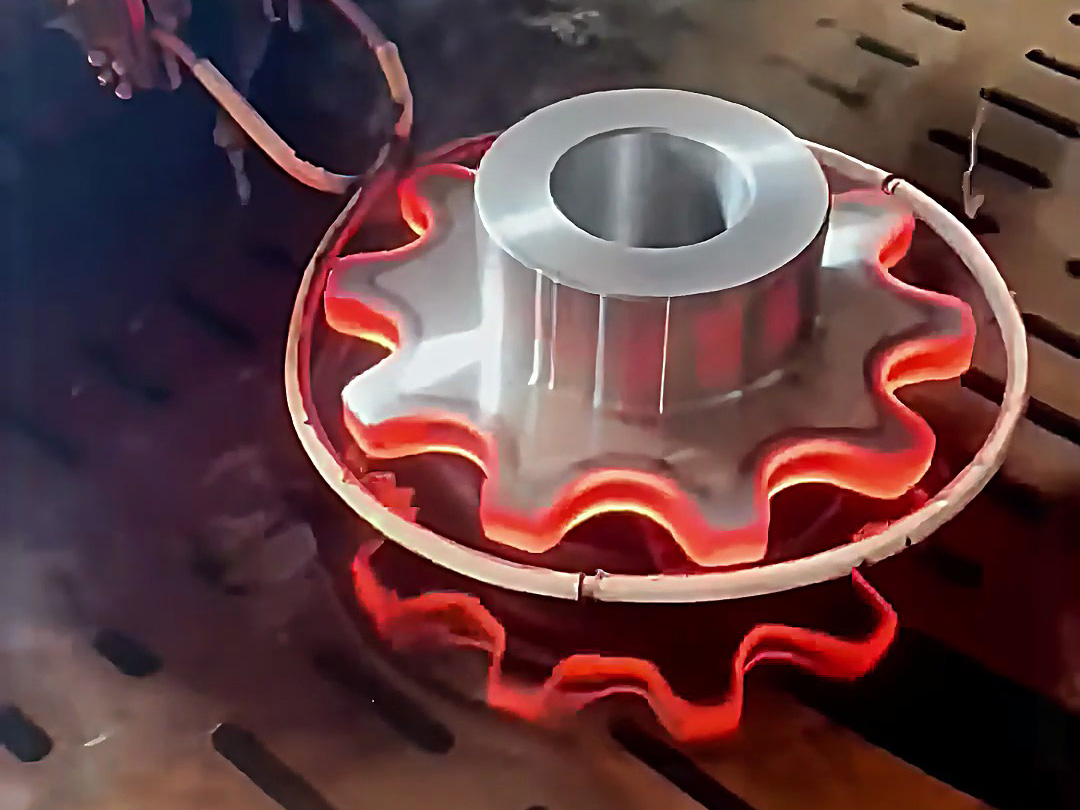
齒輪經高頻淬火后,性能優化體現在多方面:
表面硬度:20CrMnTi 等滲碳齒輪鋼齒面硬度可達 HRC58-62,較未淬火狀態(HRC20-25)提升 2 倍以上,耐磨性顯著增強;
抗疲勞性能:齒根處形成 100-200MPa 的殘余壓應力,抵消嚙合時的交變拉應力,接觸疲勞壽命延長至原來的 2-3 倍;
沖擊韌性:芯部保持 HRC30-35 的韌性,在過載或沖擊工況下(如汽車起步、換擋),齒輪不易斷裂。
某汽車齒輪廠的測試數據顯示,經高頻淬火的變速箱齒輪,在 10 萬公里路試后,齒面磨損量僅為傳統淬火齒輪的 1/3,故障率降低至 0.5% 以下。

高頻淬火設備的適配性廣泛,尤其適合:
汽車、摩托車傳動系統中的圓柱齒輪、錐齒輪;
機床變速箱內的精密齒輪(模數 1-6mm);
工程機械中的重載齒輪(需局部硬化)。
工藝實施中需注意:
線圈設計:根據齒形定制 “仿齒線圈”,確保每個齒面加熱均勻(間隙 2-3mm);
冷卻控制:采用噴霧冷卻(壓力 0.2-0.3MPa),保證齒面馬氏體轉變充分,硬化層深度控制在 0.8-2mm(模數越大,硬化層越深);
設備維護:每周清理線圈內的氧化皮,每月校準加熱功率與時間的匹配性(確保同批次齒輪性能一致)。
高頻淬火設備通過對齒輪關鍵區域的精準硬化,在保證效率與精度的同時,實現了 “耐磨齒面 + 韌性齒芯” 的性能平衡,成為齒輪制造中兼顧質量與成本的優選方案,直接影響齒輪傳動系統的可靠性與使用壽命。若需針對特定齒輪類型(如異形齒、大模數齒輪)定制淬火方案,可隨時咨詢工藝細節。